.jpg?width=1920&height=1080&name=vision%20systems%20header%20(1).jpg)
Vision systems for advanced industrial quality control
Machine vision systems for optimizing production processes and automating manual quality control
How do vision systems improve product quality and efficiency?
Vision systems - also known as machine vision or computer vision - are advanced technologies that use hardware (cameras, optics and computers) and software (algorithms and machine learning networks) to perform inspections and measurements in industrial production.
The systems are designed to recognize shapes, colors, and positions to identify defects, categorize parts, or control automated processes. Advanced vision systems can find faults and defects that are not immediately visible to the human eye.
In industrial automation, machine vision systems are often used to optimize production processes, including quality control, sorting and robot guidance. A vision system can often replace a manual inspection because the system can deliver a level of precision and consistency in the inspection that manual inspectors have a much harder time with.
By automating inspection processes, vision systems reduce the time that would otherwise be spent on quality control. At the same time, human error is minimized, ensuring higher and more consistent product quality. The precision of inspection ensures that defective parts do not pass through production and that good parts are discarded in the event of an error, which increases quality and lowers production costs.
Which industries can benefit from vision systems?
Machine vision systems are used in a wide range of industries - at JLI vision we have created solutions for:
- The pharmaceutical industry
- The wood industry
- The glass industry
- The steel industry
- The building industry
Advanced vision systems can operate in very challenging production environments and there are a wide variety of use cases. For example, systems will be very useful in these scenarios:
Production lines that produce a high number of items per hour.
With a high production frequency, it is difficult - often impossible - for manual inspectors to maintain a sufficiently high-quality inspection.
Products where quality is crucial.
If the quality of the products is critical - examples could be anything from medical devices to railroad tracks - a machine vision solution will often deliver better results than manual inspection.
High-value products.
If the value of the products is high enough, there is often a good business case for minimizing waste.
Products where defects are hard to see with the human eye.
This could be surface defects, stresses in glass, microscopic cracks or similar.
What types of vision systems are there?
Vision systems can be categorized in several ways, both in terms of their complexity and the type of inspection performed.
First, there is a distinction between 2D and 3D vision systems. 2D systems are suitable for tasks such as pattern recognition, object identification, and size measurement - all tasks where you need to "count pixels" - while 3D systems are used for more complex applications that require spatial understanding, such as cracks or other surface defects that are not visible in a standard 2D image.
There is also "traditional vision", which is based on an algorithm programmed to find specific defect types, versus vision systems based on artificial intelligence, where advanced neural networks are trained to identify and classify many different defect types at once.
The most robust solutions often consist of combinations of multiple technologies - for example, traditional 2D vision combined with machine learning. In this way, "hybrid vision" - as we call it - is created, which, through solid engineering, brings the best approaches together.
In addition, it makes sense to distinguish between standard machine vision and customized solutions. For simpler inspection tasks, it is possible to buy standard solutions that include both hardware and software in one package, making it relatively cheap and easy to get started with visual inspection.
However, if the type of quality control to be performed is more complex, a customized solution adapted to the specific use case will often be required. Learn more about how far you can get with a standard machine vision solution here.
AI and machine learning in vision systems
Artificial intelligence has the potential to be a game changer in industrial quality control because it makes it possible to solve inspection tasks that have previously been impossible - or at least disproportionately expensive - to develop a solution for.
This often involves inspecting an organic material for defects that the trained eye can assess from years of experience, but which are difficult to describe accurately enough for a classic algorithm to be effective. Often because there are multiple factors at play at the same time.
Read more: 3 real-life examples of how AI can improve quality control
However, it's important to keep a critical eye when considering the use of artificial intelligence, because sometimes it's faster and cheaper to use traditional methods. For example, when it comes to measuring quantities or determining whether a clearly defined error is present or not.
Read more: AI in machine vision - game changer or hot air?
Machine learning is often referred to as one thing, but in reality it is a range of different models and techniques, and it is important to be able to assess which type of machine learning to apply to a given inspection task.
Learn more in this edition of the video series The Vision Lab:
What is the best way to implement a vision system?
At JLI vision, we have over 30 years of experience in developing and implementing vision systems, and we have a proven model for doing so. It essentially contains the following phases:
- Project clarification. We help determine the scope and complexity of the task.
- Collection of test items. We need a range of items from production that we can test on.
- Concept development. We start building concepts so we can test how best to solve the task.
- URS - User Requirement Specification. We help define the specific requirements for the system.
- Offer a turnkey solution. Based on the URS, we create a quote for a complete solution.
- Development and production. We purchase hardware, develop algorithms and build the agreed solution. The phase ends with a FAT (Factory Acceptance Test)
- Installation and training. We install the system and train operators in its use.
If you want to know more about how a good vision project unfolds, read our guide:
How much does a vision system cost?
The price is determined by the complexity of the project, which depends on a wide range of factors that together make up the complexity of your project, and therefore the approximate cost of solving it.
The cost depends, of course, on the hardware required (cameras, lights, computer, etc.) and the software to be used. The biggest item, however, is the engineering hours needed to develop a robust, customized solution.
Generally, there are two outcomes. Either your inspection task can be solved with a standard solution or a customized solution needs to be developed.
- The price for standard solutions often starts at around 30,000 euros.
- Development tasks of medium complexity typically cost from 60,000 euros.
- Complex development tasks start at around €100,000.
We have developed a simple test that can give you an idea of how complex your inspection task is and what it will cost to solve it. Try it here.
Book a meeting to find out how you can use our vision systems in your quality control
.png)
Send me an email at hb@jlivision.com
or book a meeting and let's find out how we can help you,
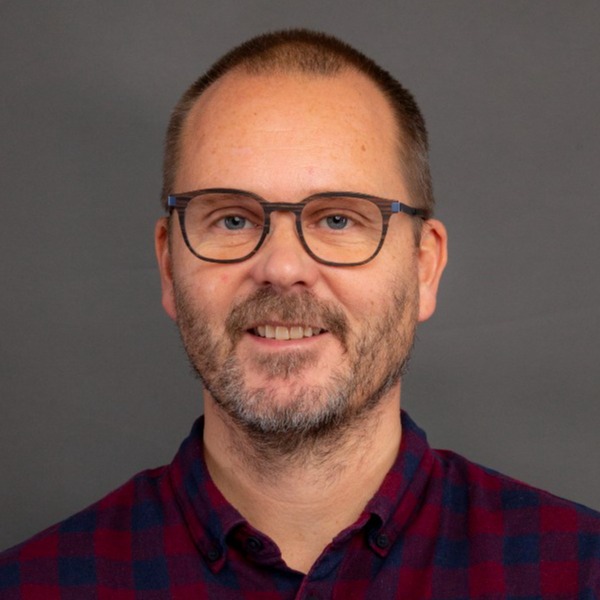