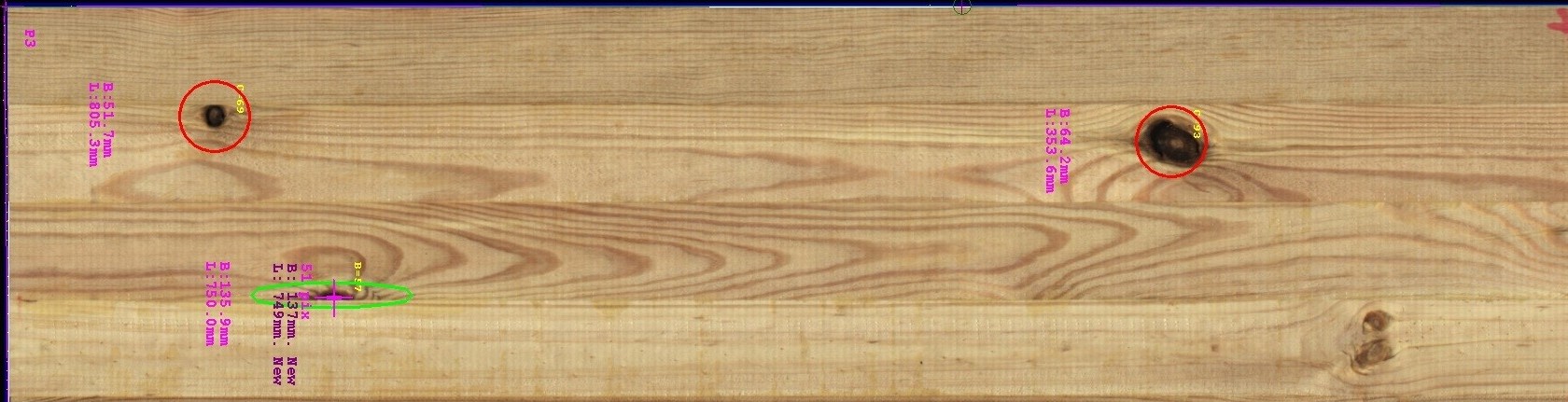
AI vision systems
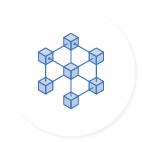
Improving efficiency and flexibility with AI
At JLI, we specialize in using AI to create powerful vision systems.
AI in vision systems opens up new possibilities for improving accuracy and efficiency. While a traditional machine vision system is designed to detect specified defects, artificial intelligence adds a layer of flexibility and efficiency by being able to handle a greater variation in defects.
We use machine learning, specifically deep learning, to mimic human intelligence through neural networks. This enables vision systems to handle challenging applications - like inspecting products with subtle variations or difficult surfaces.
There is a wide range of AI applications within vision systems, with maybe the most obvious one being the detection of aesthetic defects in surfaces that would normally require a trained eye to evaluate.
Extensive AI experience and a solid process
One of the pitfalls when trying to implement artificial intelligence is to reduce it to simply being a matter of code.
Of course, the machine learning model is key, but without the entire infrastructure in place around it, a well-functioning and robust system will not be possible.
At JLI vision, we have been working with AI, machine learning, and deep learning for several years and have built a strong process for system design, development, and deployment of AI models and continuous improvement of the system.
As an end-to-end integrator, our work with AI in vision solutions involves the 3 phases below:
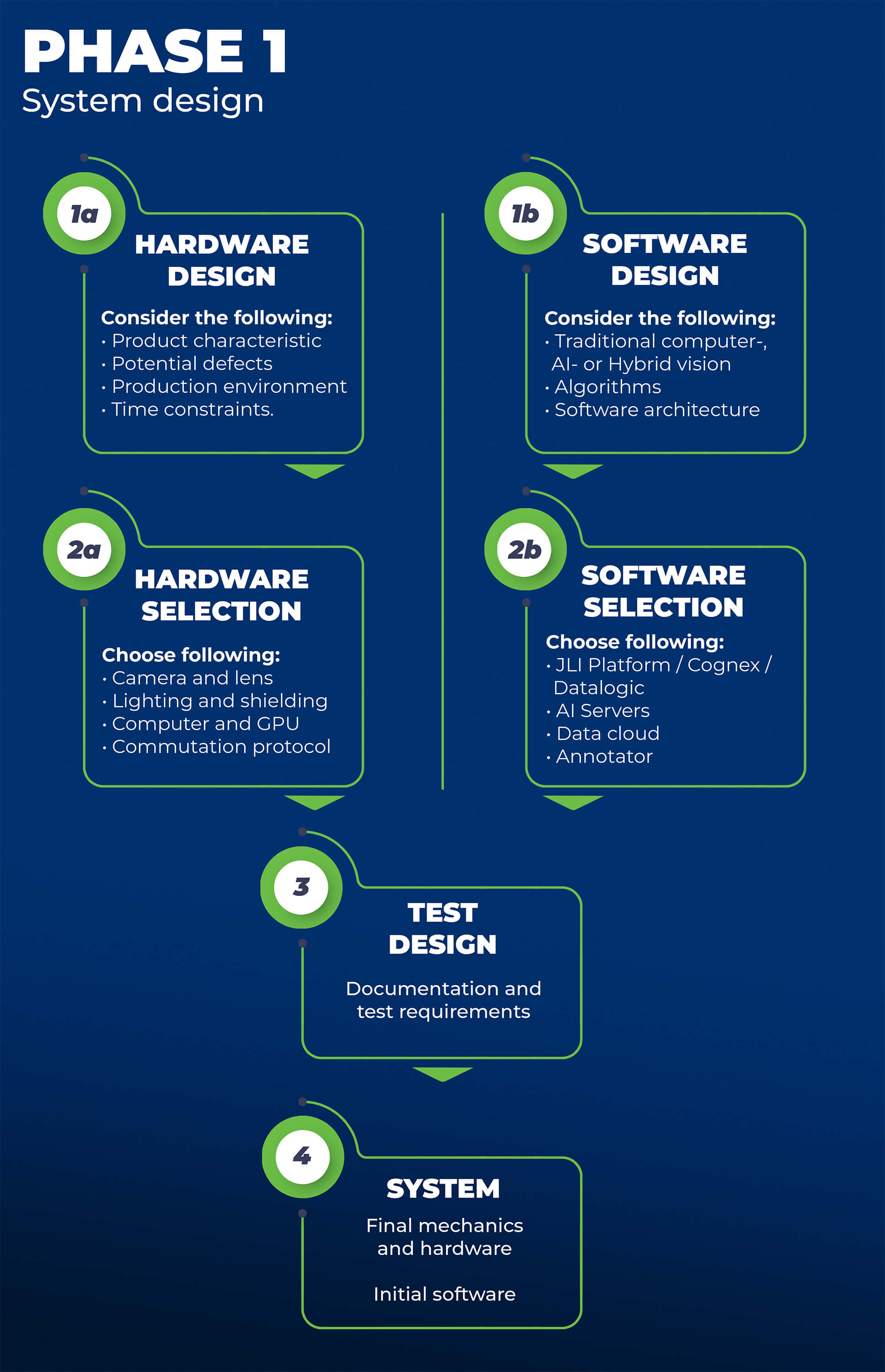
System design for AI in vision systems
The system design phase is critical as it defines the foundation for the vision system. This is where we decide on which hardware we should use to solve the task at hand - from camera and light to GPU - and also define which path to choose in terms of software.
Can we solve it with traditional computer vision, or is AI the way to go? Or should we choose a hybrid vision approach?
If we opt for AI, the system design phase includes choosing the best-suited machine learning method for the task, e.g., classification, instance segmentation, or anomaly detection.
This phase also includes choosing between using standard smart cameras or our own JLI platform.
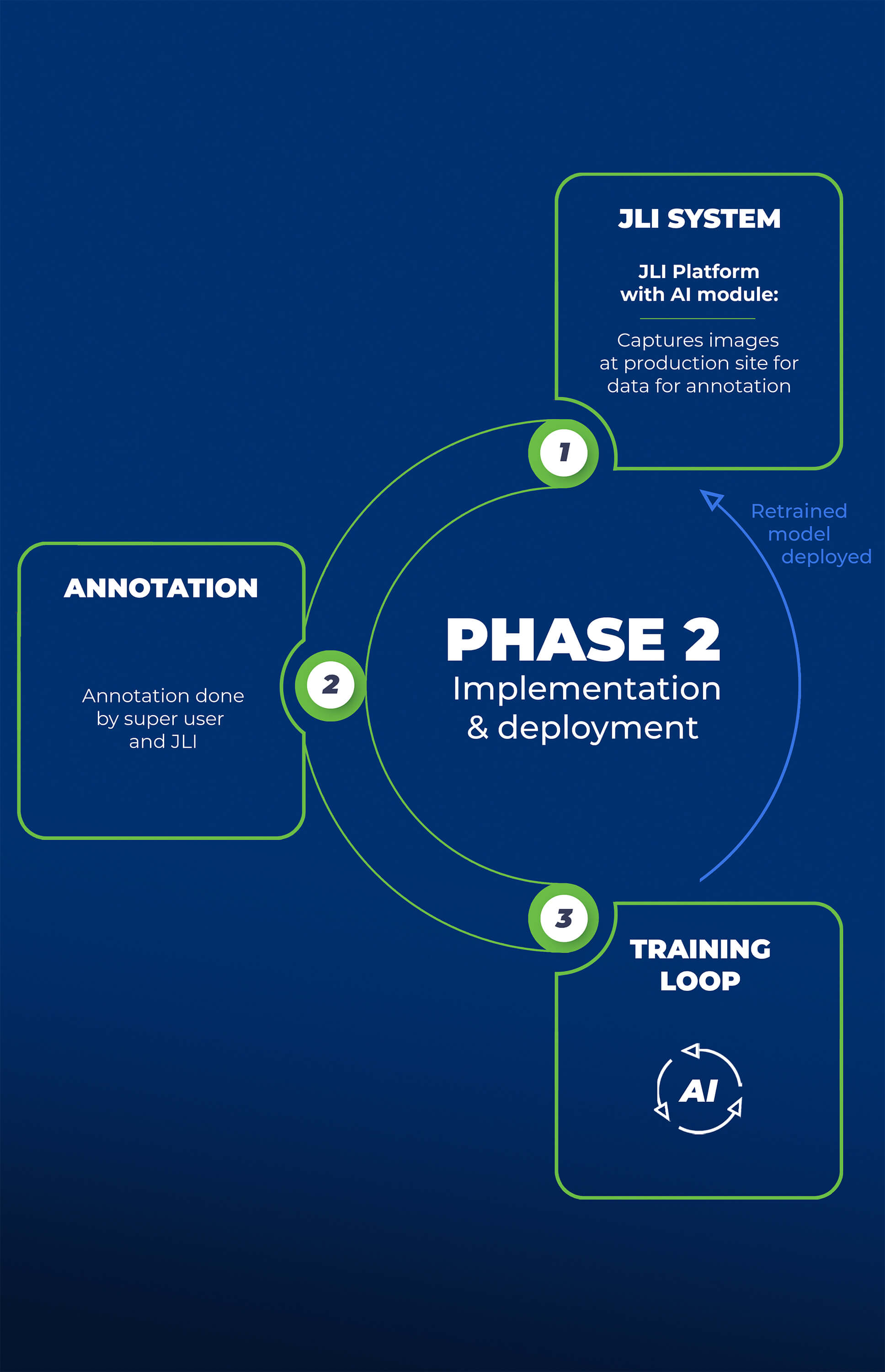
System implementation and deployment
In phase 2, we implement the specified system on the production line to start collecting images for training the AI model. Image preprocessing is often important for optimizing the model's performance.
In this phase, we annotate the images to be included in the model training material. We use the customer's professional insight into the types of defects we need to find and our own expertise in annotation to ensure that the model is continuously improved.
It is important to present the model with a variance that is representative of the actual production in this phase in order to develop an effective model.
Phase 2 is an iterative process in which we collect images, annotate them, train the model, implement the optimized model, evaluate the result, and then repeat the process until we have an AI model that delivers the desired performance.
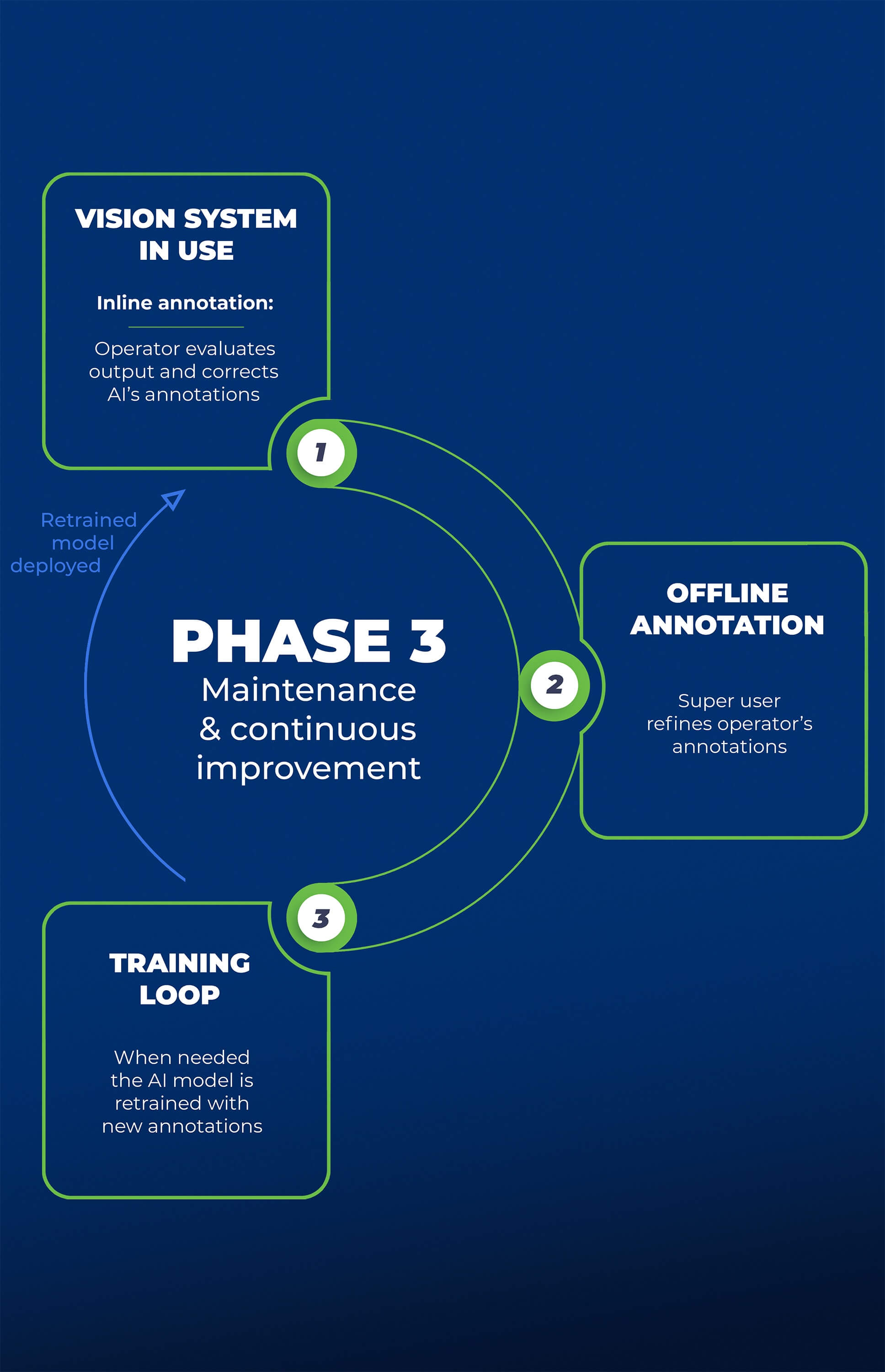
Maintenance and continuous improvement
In phase 3, the system is now deployed and inspecting inline on the production line.
Using our annotation tool JLI Annotator, an operator can inline annotate the images that the vision system delivers as output if, for example, there is a variation of defects that the model has not been trained on.
Images can then be sent for offline annotation, where a super user validates or refines the operator's annotations.
The annotated images can then be uploaded to JLI's AI server, where the model can be retrained on the new images and adapted to changes or variations in production.
We can also detect input drift and save anomalies from anomaly detection in order to train the system on these images.
This process ensures that the model is continuously improved and adapted to the current production environment.
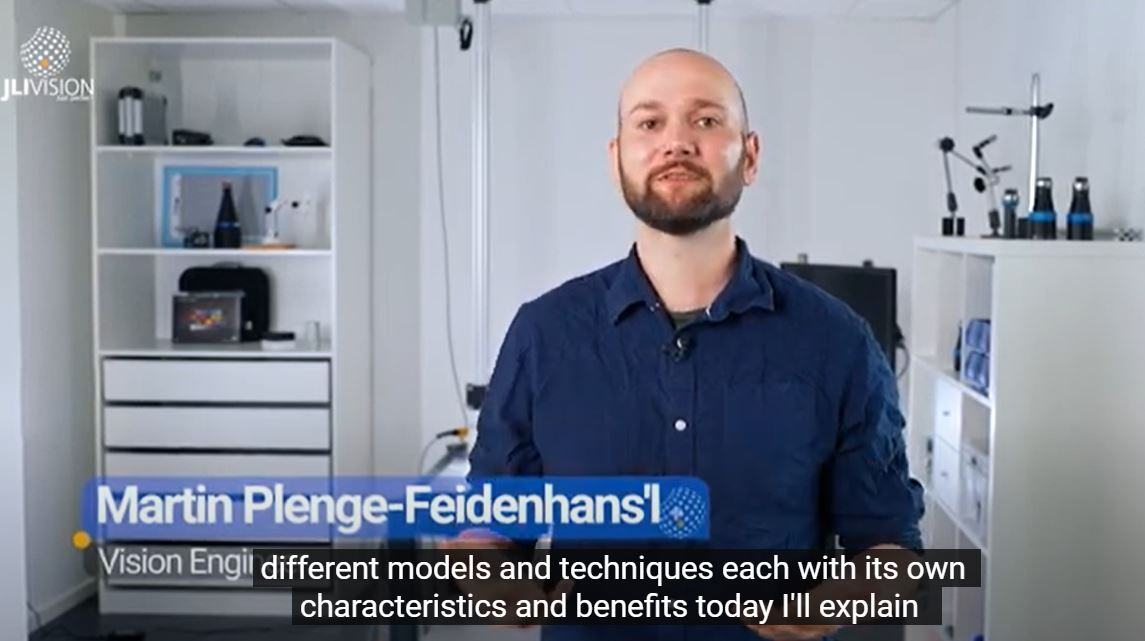
.png)
Choosing the right AI approach for your vision project
When working with AI vision systems, we use machine learning, which is often referred to as one thing. However, it consists of a range of different models and techniques each with its own characteristics and benefits.
In this video, Vision Engineer Martin Plenge-Feidenhans´l explains three of the machine learning techniques we use to improve industrial quality control:
- Classification
- Segmentation
- Anomaly detection
Application examples of AI in vision systems
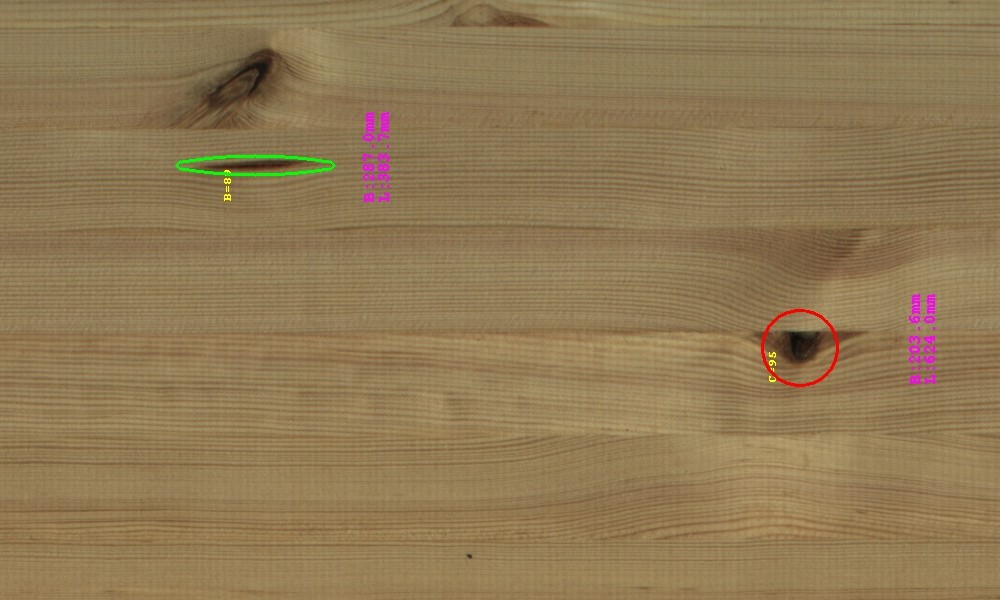
Wood inspection
Objective: Detection of gnarls and resin pockets in glue boards.
Solution: Glue Boards are scanned on a conveyor and processed using a combination of deep learning (determines if the candidate is defective), traditional machine vision (selects candidates), and 3D (checks the surface of glue boards).
Benefit: Solves a time-consuming manual inspection task inline in production and enables fully automatic repair of glue boards.
Result: Achievable accuracy +95%, which is far better and more consistent than manual inspection.
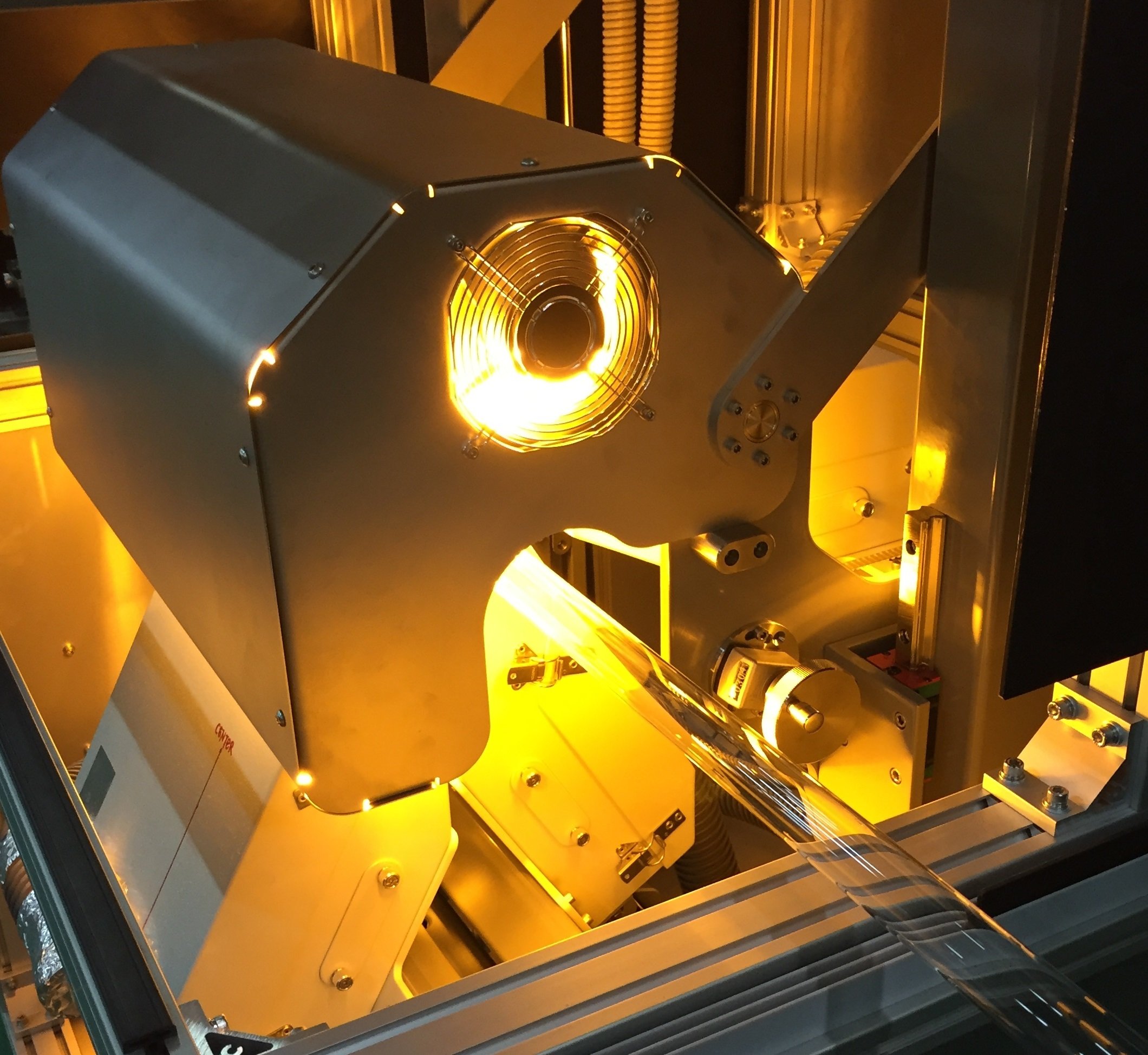
Glass inspection
Objective: Detection of open- and closed-end airlines in glass tubing.
Solution: Using traditional machine vision, all airline defects are detected. Defects are then in real-time processed by a deep learning model in order to determine whether the defect is open- or closed end.
Benefit: Improves yield by reducing scrap.
Result: Achievable accuracy +95%
.png?width=1000&height=750&name=Rail%20(Custom).png)
Steel inspection
Objective: Detection of freak defects on the surface of rails directly after production.
Solution: Rails are scanned by passing through an inspection tunnel. Images are processed in real-time using a combination of deep learning and traditional vision technology. The deep learning network is taught unsupervised.
Benefit: Solves a time-consuming manual inspection task in-line in production.
Result: Achievable accuracy +90%, which is better and more consistent than manual inspection
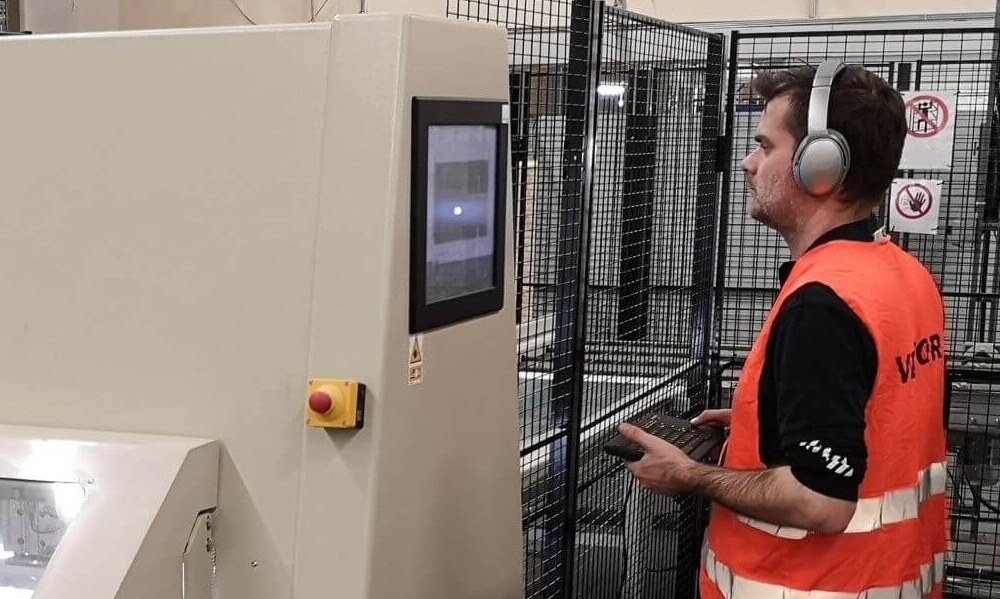
Automating a complex aesthetic inspection task with AI
Book a meeting and let's discuss how we can help
.png)
Send me an email at hb@jlivision.com
or book a meeting, and let's find out how we can help you.
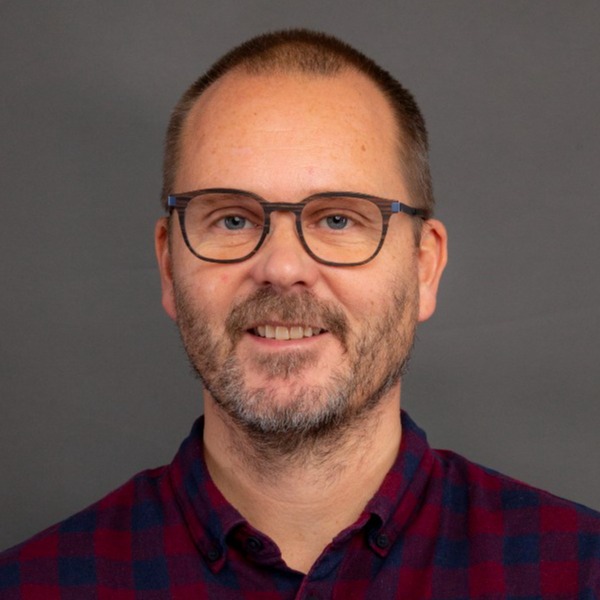