Inspection in the wood industry
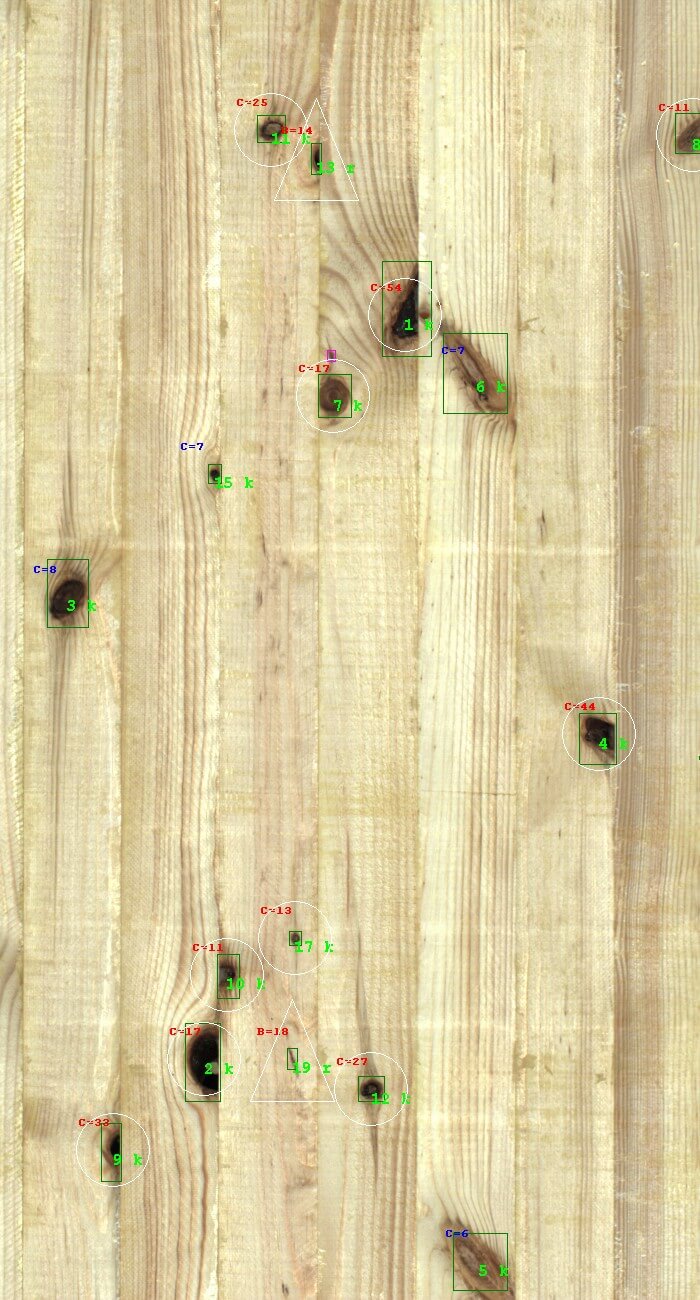
Automating a complex aesthetic inspection task
“How can we automate the inspection of glulam boards in our production line?”
That was the simple question one of the world’s largest wood and furniture manufacturers was looking to answer.
The solution, however, was less straightforward, as the inspection at hand relied on the subjective evaluation of defects like knots and resin pockets.
Before working with JLI vision, the manufacturer would have a number of people visually evaluate each board and mark defects for repair. This was a time-consuming and costly process which at the same time resulted in inconsistent quality.
The manufacturer wanted to eliminate the human factor and produce better quality.
Combining advanced machine vision with machine learning
Solving this problem required a more advanced setup than a traditional machine vision application - what JLI vision refers to as “hybrid vision”.
To replicate the human evaluation of the knots and resin pockets in the boards, JLI vision applied machine learning by processing 30,000 images of both approved and rejected items in order to train the system to be able to distinguish defects.
The machine learning network was incorporated into the scanner system, JLI vision built to inspect the glulam boards on both sides.
During inspection, the boards are transported on two conveyor belts that move at approximately 0.5 m/s. In the small gap between the two conveyor belts line scan cameras in combination with 3D cameras scan and map out both the front and the back of the board.
The human inspection process included touching and feeling knots to determine if they were at risk of loosening. This would obviously not be possible with machine vision, but by creating a 3D image of the surface, JLI vision was able to determine which knots would fall in that category.
If a defect is detected the board is directed to a repair line, where the defect is repaired according to the images created by the scanner system.
"Not only has the overall inspection quality increased, but the ROI is also impressive"
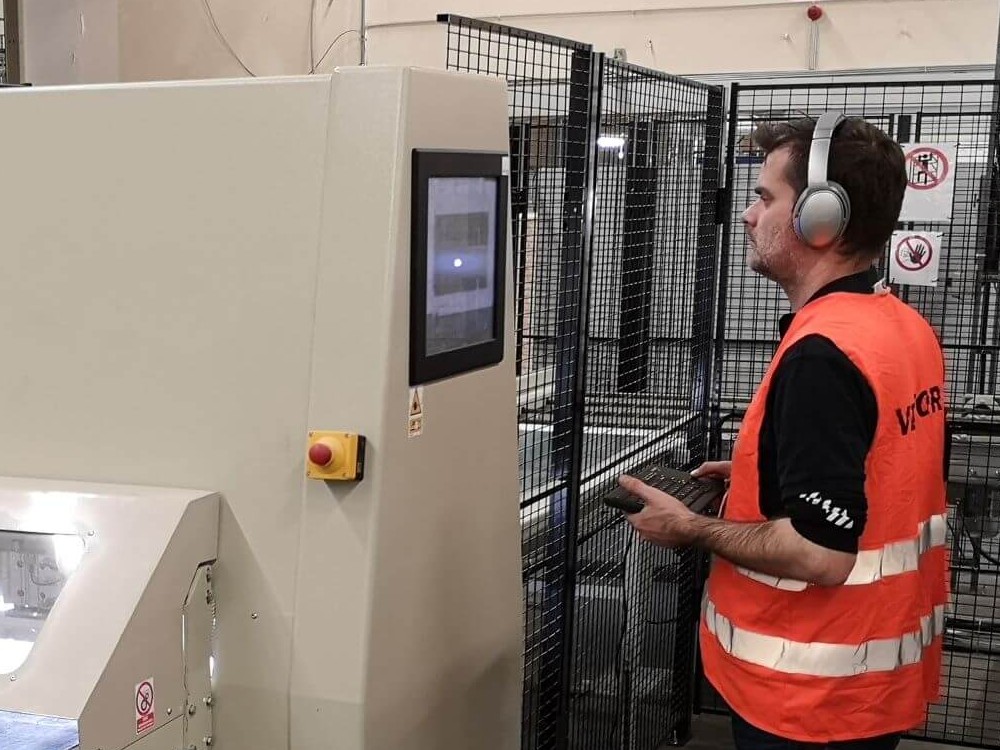
Higher quality and
impressive ROI
Some human inspection of aesthetic applications is believed to have a 70-80% accuracy.
In this case, the hybrid vision system by JLI vision accomplishes an accuracy of 98% - well above the success criteria the customer initially set for the project. Providing both consistent results and a higher quality of the end product.
“Not only has the overall inspection quality increased, but the ROI is also impressive,” says the customer’s project manager:
“JLI vision helped us automate a manual inspection task. They did it with dedication and persistence. Going from manual to automatic inspection is definitely the way forward for us and the wood industry in general.”
.jpg?width=1440&height=696&name=Group%2050%20(1).jpg)
Download the case study
Can we help you, too?
.png)
Send me an email at hb@jlivision.com
or book a meeting, and let's find out how we can help you.
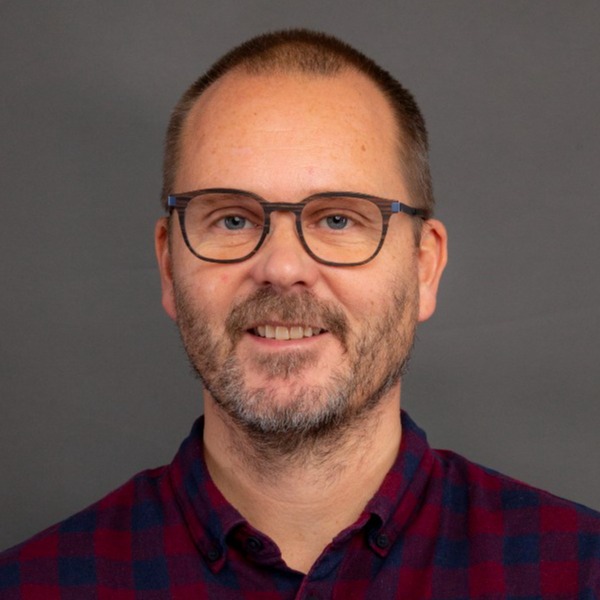