Qubiqa
.jpg?width=2034&height=1474&name=Insulation%20(1).jpg)
.png)
Achieving robustness in changing conditions
Qubiqa is one of the largest manufacturers of machinery for the insulation industry in the world.
In industrial machine vision, it is often crucial that the scene of inspection is under control.
Sometimes this isn’t quite as easy as you would want it to be. In these cases, you have to be innovative and find solutions that do not compromise the quality of the installed inspection system.
One of the tools that can help you achieve robustness under changing scene conditions is advanced pattern recognition.
Advanced pattern recognition may allow you to incorporate significant changes in lighting conditions and also adapt to acceptable changes in the product you are inspecting.
Checking the orientation of insulation packs before unitizing faces both changing light conditions and mats looking slightly different from time to time.
“Using state-of-the-art pattern recognition JLI provided us with a solution that works robustly in a variety of conditions and on top of that is flexible."
Morten Øllgaard Bloch, Project Manager, Qubiqa
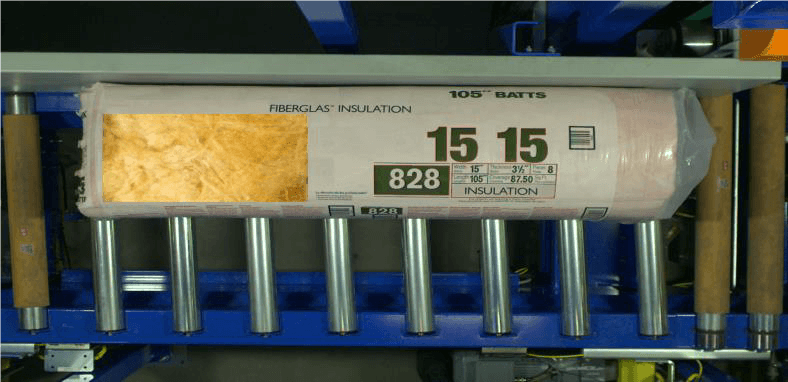
A robust system for harsh production environments
Qubiqa needed a flexible and robust system that examined the orientation of packs and was able to cope with damaged or dirty bags.
The harsh production environment at an insulation plant also requires a focus on proper system design, so dust and high temperatures do not challenge long-term performance.
The system should be general and allow new products to be “taught”.
“JLIs solution has helped us solve an inspection task where we do not have in-house competencies. JLI provided a generalized solution that can be reused in other projects in the future. We will not hesitate in using JLI again.”
Morten Øllgaard Bloch, Project Manager, Qubiqa
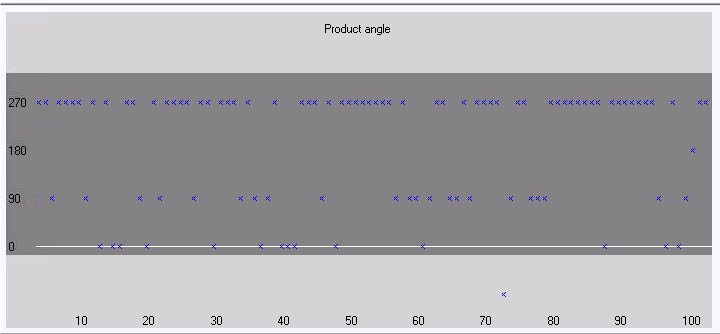
Color imaging and advanced pattern recognition algorithms
JLI vision designed and manufactured an inspection system that inspects the print on the insulation bags.
It uses color imaging and advanced pattern recognition algorithms, to verify the appearance is acceptable and matches what the customer expects. Product mix-ups are checked.
Before a batch starts, training is performed on the appearance of the insulation bag. During production, the orientation will be random, but the vision system measures the actual orientation.
The unitizing machine is now able to produce uniformly presented products.
.jpg?width=1440&height=696&name=Group%2050%20(1).jpg)
Download the case study
Can we help you, too?
.png)
Send me an email at hb@jlivision.com
or book a meeting, and let's find out how we can help you.
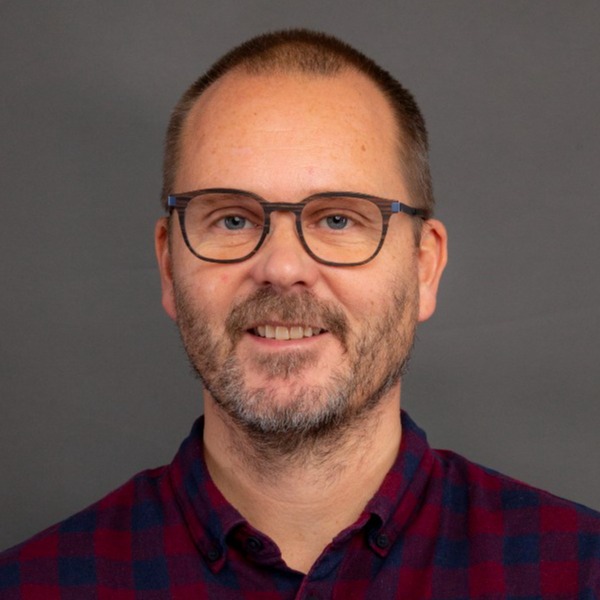