Smurfit Westrock
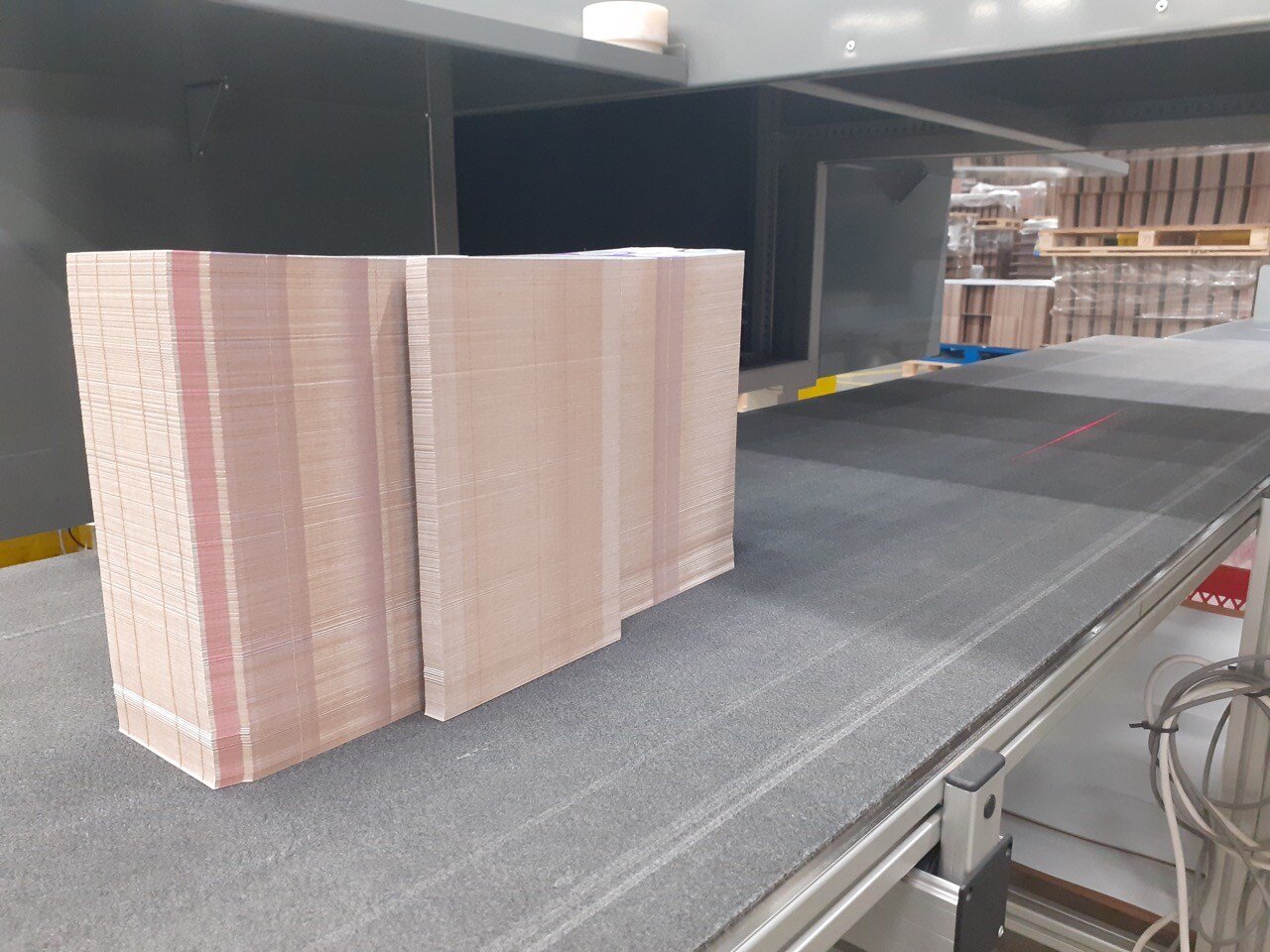
Complex color inspection of up to 1.000 items at a time
To meet a customer requirement for quality control, Smurfit Westrock needed to find an efficient way to automate the inspection of large stacks of cardboard packaging.
Smurfit Westrock is a global leader in sustainable packaging, operating in 40 countries with more than 100,000 employees.
Smurfit Westrock supplies cardboard packaging for a nutrition product to Danone, among other things, and this production required a quality inspection.
The packaging is marked with specific colors to match certain contents, and the quality control had to ensure that there was no critical mixup of the different types of packaging.
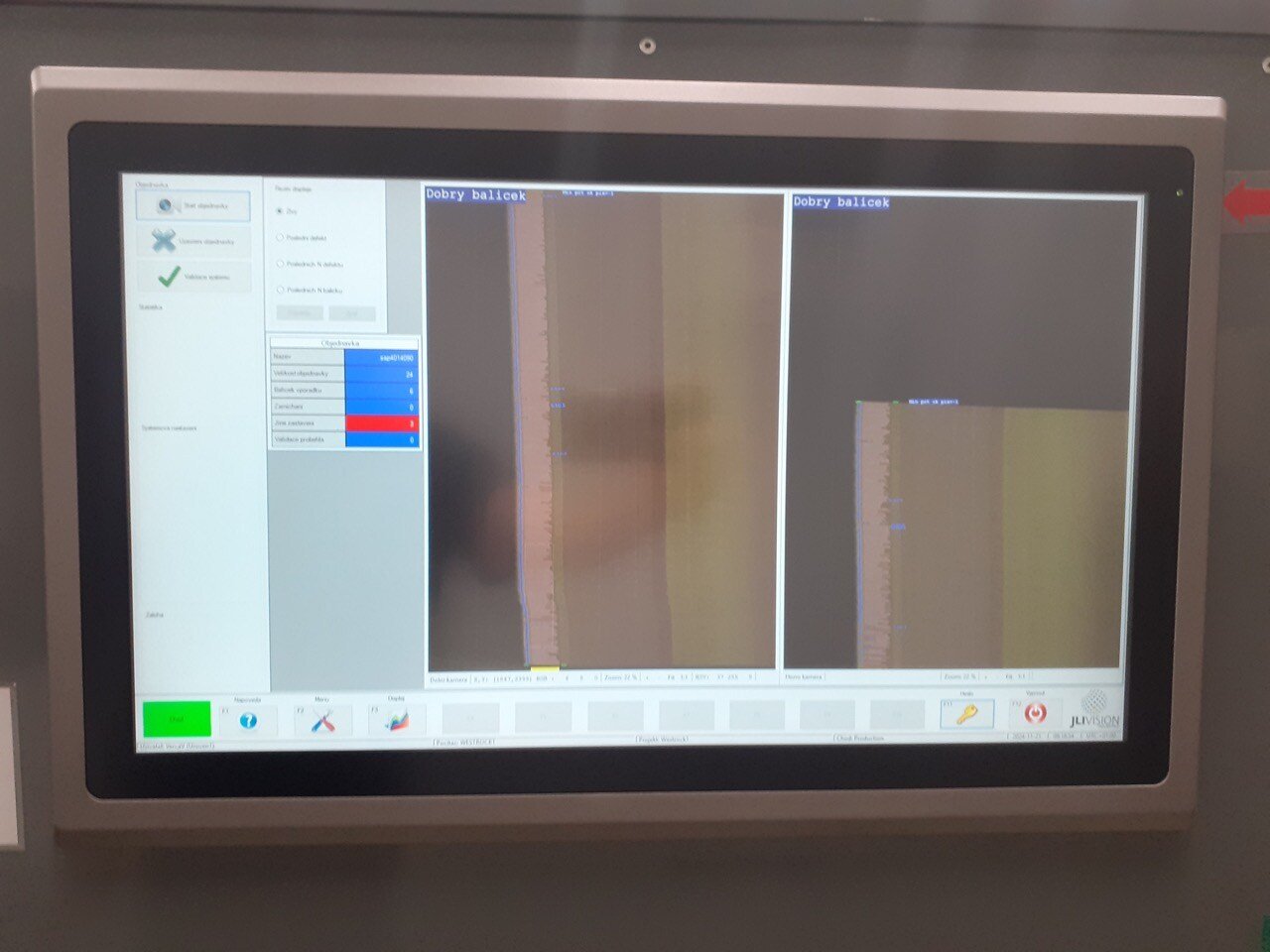
The task of automating the visual inspection was complex for several reasons:
- The stacks of cardboard are large, so up to 1000 cards need to be scanned at once.
- The colored eye mark, which defines the product type to be checked, is not placed on the side of each card, but on the top, so only a minimal strip of colored material is visible.
- The stacking is not aligned perfectly, as each card can be shifted a bit in the stack. In a naive light and camera setup, the cards could occlude or cast shadows on other cards.
- The packaging surface is glossy, which can cause reflections. Direct reflections would have the color of the light source instead of the color of the eye mark.
“The device has been developed as per a request for Danone nutrition packaging as the last stage of the quality control system before the packs are released to the customer.
The packs are produced on the combi layouts, and the device is capable of controlling each pile after cutting and creasing and before palletizing in terms of product mix based on the colored eye marks on the flaps"
- Milan Menc, Maintenance technician/Metrologist, Smurfit Westrock
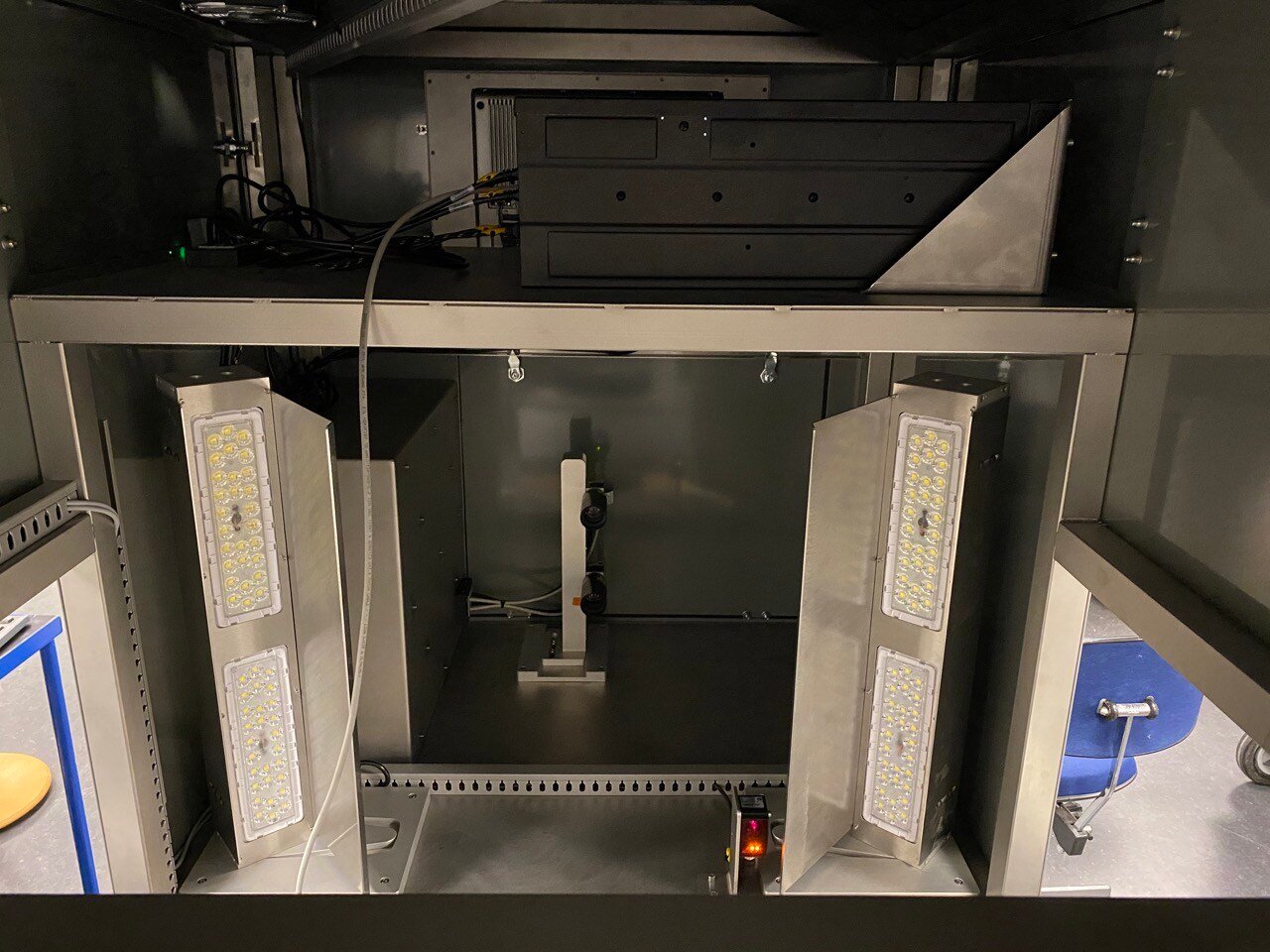
Innovative lighting and camera setup
The height of the pile, combined with the potential misalignment of some of the cardboard, calls for a special lighting solution at least as high as the pile.
To prevent shadows, an illumination with a high directionality of the light rays was chosen.
An orthographic view that allows a perpendicular view to the side of the pile was needed to prevent occlusion, and this was achieved by using optics with a high focal length, as well as multiple cameras to cover the entire pile.
To measure the exact color of the eye mark, the light and camera angles were arranged in a way that unwanted reflections were directed away from the cameras.
The cameras were color-calibrated at JLI vision’s lab, but the actual eye mark color was calibrated in the system’s training function, which includes variations in illumination and eye mark color.
To allow for future changes in production, the operators can easily train the system to recognize a new color of packaging or placement of the eye mark.
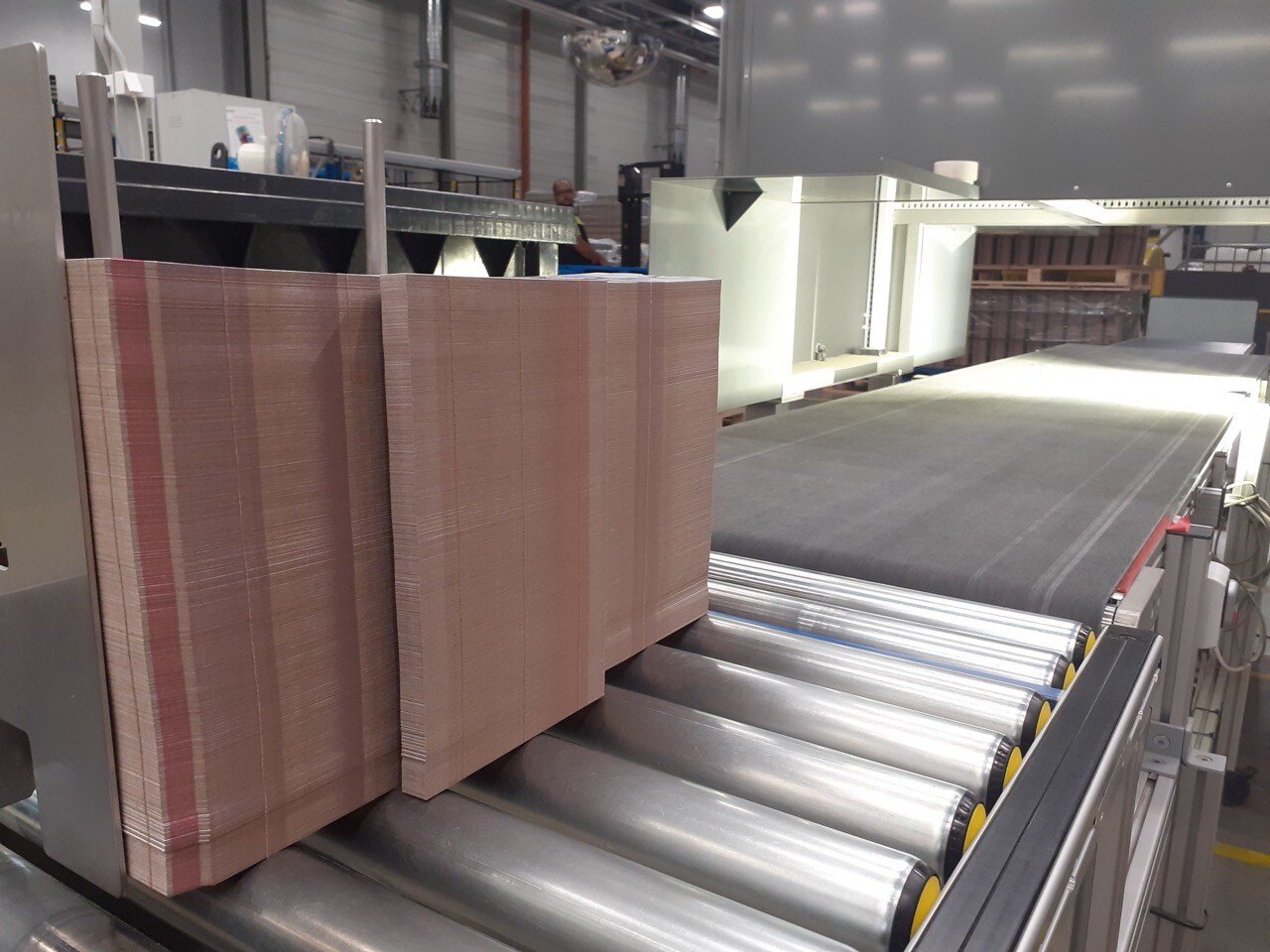
Technical data
- Number of cards in stack: Up to 1.000
- Thickness of cards: Approx. 0.5 to 1 mm
- Operators can easily train the system to recognize new colors and placement of eye mark.
- Scanning portal includes monitor, computer, light, camera, and electrical wiring.
Can we help you, too?
.png)
Send me an email at hb@jlivision.com
or book a meeting, and let's find out how we can help you.
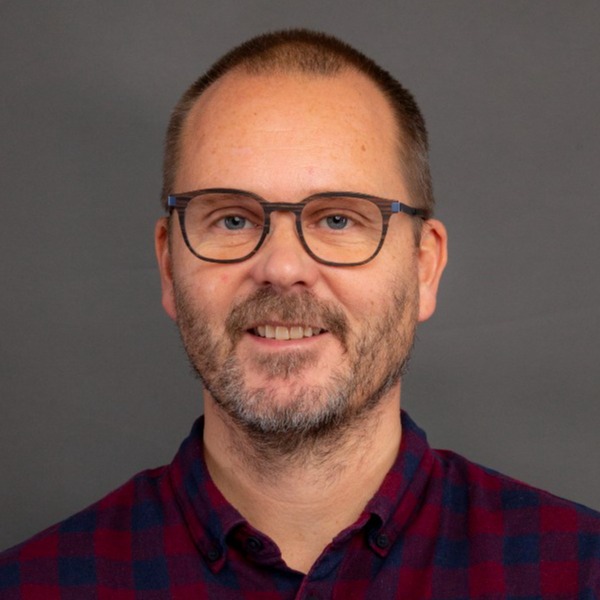