3D inspection plays a critical role in quality control, enabling precise measurements and defect detection that go beyond what’s possible with 2D vision systems. But how do you generate a 3D image of an object?
Several methods exist, each with its own strengths and limitations. The right one depends on the inspection task at hand. Below, we’ll cover four commonly used 3D inspection techniques and where they are best applied.
Stereo imaging – the traditional approach
Stereo imaging is one of the simplest and most cost-effective ways to generate 3D images. It requires just two well-calibrated cameras positioned at known angles.
By capturing two images from different viewpoints, you can triangulate the depth and reconstruct a 3D shape. This method can achieve precision down to less than 100 micrometers, making it suitable for detailed inspections.
Use cases for stereo imaging:
- Inspecting stationary objects by capturing a full 3D image
- Inspecting moving objects using a line scan camera
Limitations:
- High computational demand for processing images
- Slower than other methods since calculations are done after image capture
Structured light – high accuracy for stationary objects
Structured light takes a different approach by projecting a known pattern—such as stripes—onto an object. The way the pattern deforms provides data on the object’s 3D shape.
For even higher accuracy, a technique called time-coded structured light uses multiple patterns, increasing the number of data points available for calculation.
Use cases for structured light:
- High-precision 3D measurements
- Inspecting complex geometries where accuracy is crucial
- Capturing 3D models of stationary objects from multiple angles (e.g., using a robotic arm)
Limitations:
- Only works on stationary objects
- Requires multiple images from different angles to get a full 3D reconstruction
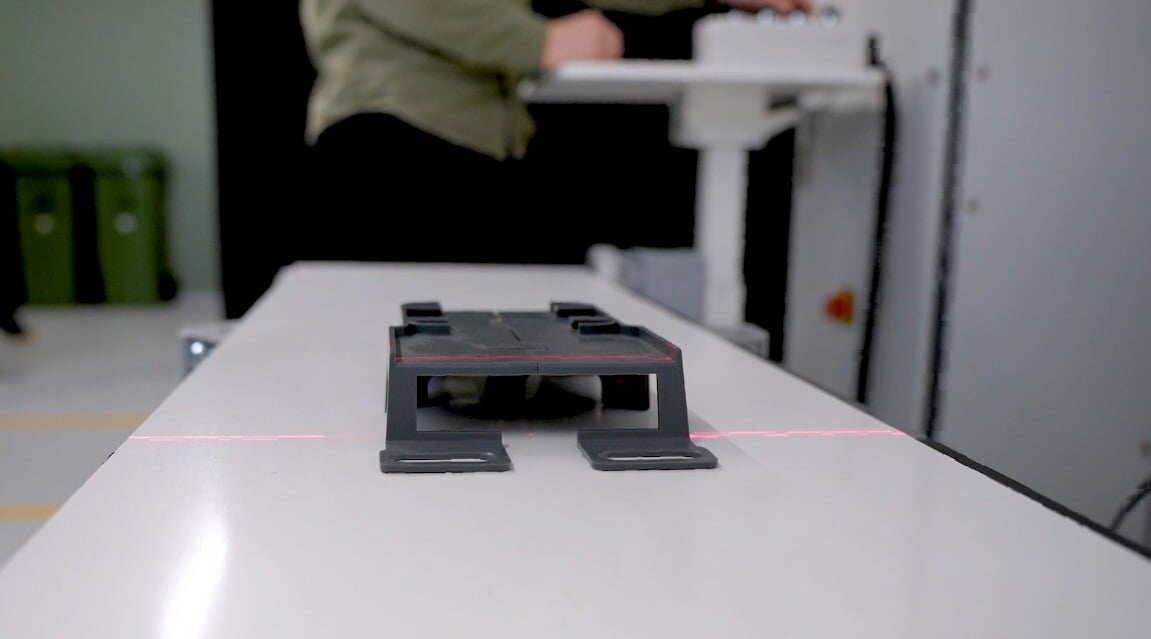
Laser profiling – fast and accurate for moving parts
Laser profile scanning, also known as laser triangulation, projects a laser line onto an object’s surface. A sensor captures how the laser deforms along the object’s contour, building a high-precision 3D profile.
This method is widely used in automated quality control, particularly for scanning objects in motion on conveyor belts.
Use cases for laser profiling:
- Fast, high-accuracy inspection of moving parts
- Measuring large components where traditional 3D scanning is impractical
Limitations:
- Requires proper shielding to prevent laser reflections, which can pose safety risks
Multi-view 3D reconstruction - AI-powered speed
Multi-view 3D reconstruction creates a full 3D shape by combining images taken from different angles. Traditional photogrammetry has been used for years, but newer AI-driven methods, such as Neural Radiance Fields (NeRFs), require fewer images while providing faster and more accurate 3D reconstructions.
NeRFs use artificial intelligence to model how light behaves in a scene, allowing for rapid 3D reconstruction with fewer input images.
Use cases for multi-view 3D reconstruction:
- High-detail 3D scanning with fewer images
- Situations where photogrammetry would be too slow
Choosing the right 3D inspection method
Each of these 3D inspection techniques offers distinct advantages. If speed is critical, laser profiling is a strong choice. Structured light may be the better option for high-accuracy measurements of stationary objects. Stereo imaging remains a cost-effective approach for many use cases, while multi-view 3D reconstruction is pushing the boundaries of AI-driven quality inspection.
The key is selecting the right method for your specific inspection needs. If you’re unsure which approach is best, we can help you evaluate the options and find the most efficient solution for your production line.